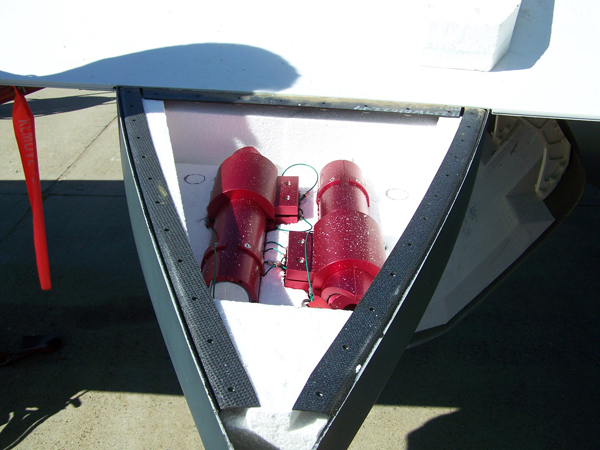
Divert Kit fits snugly in an otherwise empty space in a Global Hawk wing without affecting the aircraft performance…….(U.S. Air Force photo)
A simple solution to a difficult problem resulted in dramatically enhancing the ability of the RQ-4B Global Hawk to deploy anywhere in the world.
Because this particular aircraft requires a specialized tow bar to be moved on the ground, it is pre-programmed with a list of airfields possessing necessary ground support equipment. In the event of an emergency, the aircraft would automatically divert to one of those approved locations if it needed to get on the ground quickly.
Aeronautical Systems Center’s Global Hawk Division saw this as a limiting factor that needed to be rectified if the aircraft was to be truly “global.” “We went through several designs but could not settle on something that met our requirements in terms of time and money,” said Dave Wimer, a structural engineer in the division. “Then, our leadership decided to see if we could develop a design ourselves.”
The resulting kit, designed by Mr. Wimer, consists of a tow bar adapter and main landing gear down locks. The entire kit weighs a mere 14 pounds and costs less than $2,000 each to manufacture. It is also small enough to fit neatly inside the Global Hawk’s wing which means no expensive modification to the aircraft itself was required.
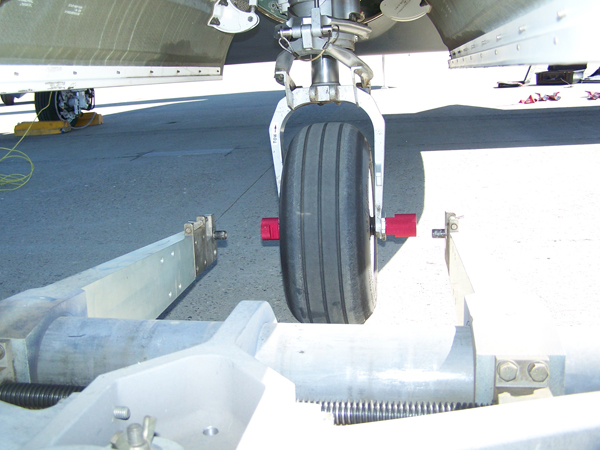
The tow bar adapter (red) allows the Global Hawk to be towed by any of the universally available tow bars found at airports worldwide... (U.S. Air Force photo)
The simple yet ingenious design allows the Global Hawk to be towed by any of the universally available tow bars found at airports worldwide. “This is the kind of innovative solution we are going to need more of in this era of tight budgets,” said Col. Karl Rozelsky, Global Hawk Division chief. “This is an excellent example of ‘doing more without more.'”
The critical, and most challenging, element for the design is the main landing gear down locks, Mr. Wimer added. “The down locks are necessary to ensure the gear doesn’t collapse during towing or when the airplane is parked, should there be a malfunction of the hydraulic system,” he said. “The down locks represent the bulk of the fly-away kit by weight and cost.”
Once the design was settled, the division contracted with a small local tool manufacturing company to produce the adapters. Mar-con Tool Co. of Moraine, Ohio, handmade 20 kits on mills and lathes in their shop. Eight of those kits are now deployed — snugly stored inside the wing’s leading edge.
The entire effort from concept to operational deployment took three weeks. “I’m proud of Dave and the rest of the team for thinking outside the box, as well as the fantastic support we received from the folks at Mar-con,” Colonel Rozelsky said.
Source: Air Force Materiel Command