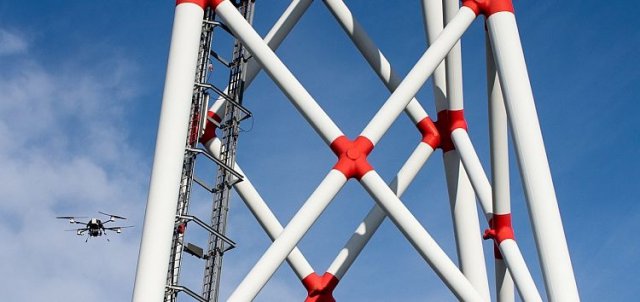
The RepaKorr project is funded by the German Federal Ministry of Education and Research and co-ordinated by Muehlhan AG. It has brought together manufacturers of coating materials, specialists in the application of coating systems, windfarm operators, companies that specialise in building steel structures, industrial safety experts and a company that specialises in mini and micro unmanned aerial systems to combine their expertise in materials science, engineering, system design and organisation to prepare the ground for a new onsite repair concept for offshore windfarms. The partners in the project are Fraunhofer Institute for Manufacturing Technology and Advanced Materials; Muehlhan AG; the industrial coatings division of Sika Deutschland; Corroconsult, Gesellschaft für Coating Control Consulting GmbH; AirRobot GmbH & Co KG; and Senvion GmbH.
Speaking exclusively to OWJ, project spokesperson Dr Andreas Momber, who works for Muehlhan, explained that the project got underway in April 2013. Asked what progress has been made so far and what are the most recent milestones in the project, Dr Momber explained that the partners in the project have tested a drone at sea and recently improved the design of that drone to enable it to fly in a stable manner in high wind speeds and to deliver high quality images. The improved drone can also now be launch and recovered safely on vessels offshore.
Asked why drones are being considered and what their potential applications are, Dr Momber noted that human-based inspections are time consuming and expensive. “And the results are limited,” he said. “In contrast, drones can follow a prescribed (programmed) flight path around an offshore structure and can repeat it as often as is required. This is a great benefit for a time-constrained based condition monitoring project. Drones deliver digital data and could even do so in real time. They are a great tool for initial screening and for inspecting critical areas of a structure.”
Dr Momber said he could not divulge details of when and where drones had been tested but said that the project partners had done an onshore test flight at a windfarm and achieved “excellent results”. He said he believes that their potential in the offshore wind industry was “significant” in the longer term. “It’s the future,” he said. “Owners of offshore windfarms are already aware of the advantages but are waiting for reliable, inexpensive equipment to be developed.” He said he believed that – as is usually the case with any innovative application of new technology – windfarm operators were waiting for a track record of successful projects to be completed before they committed to using drones. “Training pilots for unmanned aerial systems and specialists who can interpret the data and images produced is also an issue for the time being, as are data transmission and exploitation. “What should a windfarm operator do with the data delivered by the drones and with associated data such as location, photography, videos, wind speed and temperature? These are some of the issues we are planning to address in subsequent R&D projects,” he said.
“We have also developed a repair coating system for offshore applications that reduces the demands on substrate quality. It can be applied in one run with a cartridge (including mixing and metering). The coating is currently undergoing the ISO 20340 test along with a benchmark coating. The results will be available in summer. We also applied it in an offshore test on the island of Helgoland. An initial inspection delivered excellent results.
“We have investigated a number of surface preparation methods for use offshore, including rotating brushes, grinders, vacuum machines and water spray nozzles, all of which are handheld. We have also developed a two-step substrate preparation scenario for heavily corroded sections and examined all of the safety and environmental aspects of working offshore and have investigated ways to minimise the consumption of resources,” he concluded.
The potential of unmanned aerial systems has also recently been recognised by classification society Lloyd’s Register (LR), which has published guidance to support safe and effective deployment of next-generation drones and unmanned aerial systems in inspections as a way to improve productivity, reduce risk exposure and in-service inspection costs and to speed up survey times. It says ‘eyes in the sky’ technology enables rapid, safe and repeatable inspections for offshore, shipping and onshore infrastructure that will offer long-term benefits to the energy and marine sectors, delivering high levels of integrity, compliance and commercial advantage.
“We are developing these guidance notes to provide a consistent approach to risk in UAS and drone deployment, offering practical operational considerations relating to regulations, personnel, quality, safety, hardware, software and operations,” says LR chief technology officer Nial McCollam. “Technology and innovation in the area of digital data, sensing technologies, unmanned systems and robotics are here to stay. We see an exciting and important journey ahead and anticipate our efforts to increase and continue.” Shipping and energy companies are seeking to use drones to make in-service operational assessments and surveys safer and more effective, especially in hazardous environments and where equipment is difficult to access. Early adopters include Shell and Maersk Drilling.
The guidance notes from LR will be updated regularly to provide industry with the latest practical information on issues such as how best to use UAS for inspection in confined spaces, which is particularly relevant in energy and marine applications where class surveys are needed and also improves safety for human life. “In the past, small commercial UAS technology can be traced back to remote-controlled hobby aircraft requiring significant skills to operate. However, rapid advancements in hardware and software including air stabilisation, pre-flight planning tools, obstacle detection and avoidance technology have transformed these small aircraft into viable business tools that is likened to high definition eyes in the sky,” says Chris Chung, head of strategic research at LR.
In March 2016, the Lloyd’s Register Foundation convened an international panel of industry and academic experts for a two-day workshop on robotics and autonomous systems (RAS) to identify current state of the art and the white space where the foundation can add significant impact and contribution in line with its charitable objectives. The review will be published as part of the Foundation’s Foresight Review series of reports later this year. The Foundation is expecting to make a significant grant investment in remote systems to deliver the findings from the report.
Source: Offshore Wind Journal