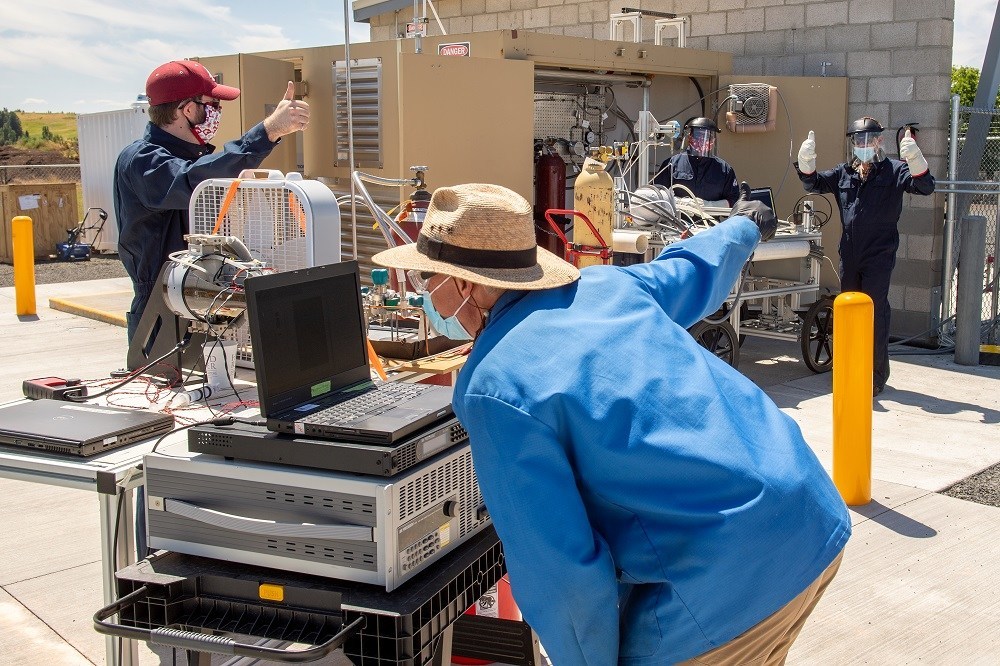
Insitu engineers worked with researchers from Washington State University and Protium to conduct successful testing of a hydrogen supply tank in July of 2020. The event marked one of the company’s many recent efforts to advance fuel cell technology for unmanned platforms.
Insitu, a wholly-owned subsidiary of The Boeing Company, has announced new details about its latest efforts to advance hydrogen fuel-cell propulsion for Unmanned Aerial Vehicles.
First Flight of Hydrogen-Electric ScanEagle3 UAV:
In December 2020, Insitu completed the first flight of the ScanEagle3 unmanned aerial vehicle (UAV) powered by an all-electric, hydrogen fueled, proton exchange membrane (PEM) fuel cell. The 30-minute flight confirmed initial performance characteristics including power output, climb rate, and intrinsic aerodynamic flight characteristics for the UAV in preparation for test flights using a Liquid Hydrogen (LH2) storage tank on the aircraft that are planned for later this year. The 3-D-printed LH2 tank is an industry first, and is expected to support 10+ hours of endurance for ScanEagle3.
Liquid Hydrogen Flight Tank for Insitu ScanEagle3 UAV Completes First Fill Test:
In February 2021, a Liquid Hydrogen (LH2) flight tank designed for Insitu’s ScanEagle3 UAV successfully completed liquid hydrogen fill, pressure and vapor generation testing at Washington State University’s Hydrogen Properties for Energy Research (HyPER) Lab. The tests verified operation performance metrics of the LH2 tank in preparation for upcoming flights of ScanEagle3 equipped with a PEM fuel cell power system. The LH2 Tank Integration project is part of a larger development effort to compare acoustic and thermal signatures of a small UAV powered with an internal combustion engine versus an all-electric power system.
“For our global Defence customers, fuel-cell-powered UAS in this Group 2 space represent a significant game changer in the battlespace,” said Andrew Duggan, Managing Director Insitu Pacific. “Operationally, fuel-cell-powered platforms provide the potential for longer endurance missions, increased power availability for payloads, as well as significant reductions in noise signature.”
The defense industry is growing increasingly interested in the benefits of hydrogen fuel cell technology, which range from environmental to operational. Fuel cells support better ISR data collection because PEM fuel cell stack emissions are limited to small amounts of H2O and trace amounts of H2. The fuel cell and electric motor thermal and acoustic signatures are significantly lower than traditional internal combustion (IC) engines, enabling mission routes closer to targets. The PEM fuel cell / electric motor combination also decreases platform vibration and enables excess power to support greater payload diversity. Fuel cells also deliver improved reliability and significantly lower logistics costs relative to small IC engine propulsion solutions.
Tests are expected to continue in Q2 of 2021 with the first liquid hydrogen flight planned for late summer 2021.
Source: Press Release