Metro Hop has the green light from the United States Air Force Agility Prime program to test its patent pending Active Landing Gear. This unique landing gear allows Metro Hop’s all-electric, short takeoff and landing (eSTOL) aircraft to fly up to 250 mph with substantial payloads, while operating nearly silently out of small spaces.
This landing gear also means that the Metro Hop aircraft can handle most vertical takeoff and landing (VTOL) missions with superior performance.
With this Phase I Small Business Technology Transfer contract from Agility Prime, Metro Hop is teaming up with Auburn University’s Vehicle Systems, Dynamics, and Design Lab (VSDDL) to model and validate the design of the Active Landing Gear. VSDDL will use its flight simulation facilities and software to model the gear under various conditions during the takeoff and landing phases of flight.
“The VSDDL recently developed a reconfigurable flight simulator aimed at novel aircraft configurations and we’re currently developing two more. We look forward to using our capabilities to give us precise measurements of Metro Hop’s flight capabilities and allow us to aggregate essential data on the plane,” said Dr. Imon Chakraborty, assistant professor in the Department of Aerospace Engineering at Auburn University and director of the VSDDL.
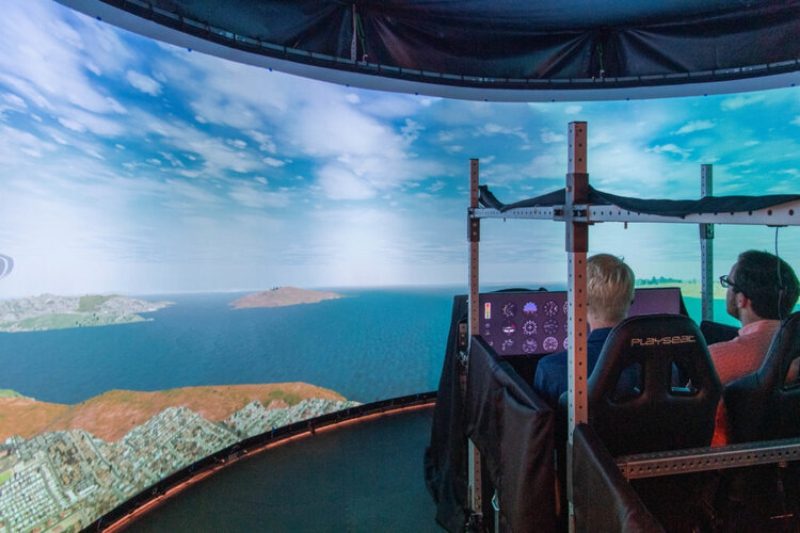
The Vehicle Systems, Dynamics, and Design Laboratory Reconfigurable Flight Simulator at Auburn University
After this initial phase of testing is completed, Metro Hop will move forward with construction of a fully operational landing gear set and begin dynamic landing-drop and taxi testing.
“We are grateful for this support from Agility Prime and we are thrilled to be working closely with the VSDDL team at Auburn University to move our project forward,” said Metro Hop CEO and Founder Bruno Mombrinie. “This is the first step among many: let’s fly!”
Metro Hop envisions using a rubberized takeoff/landing mat with the subscale prototype it intends to build. The traction and smoothness of the surface could suit non-runway environments, shortening a takeoff run for the proposed prototype to just 100 feet Mombrinie says.
An eventual full-size airplane could use conventional runways or a more permanent prepared surface with rubber tile operationally while the mat option could work in pop-up scenarios.
If such a gear design/landing surface combo can effectively shorten the takeoff and landing runs of electric airplanes, it could find favor. Taking off conventionally requires less power than taking off vertically like numerous UAM aircraft are now being developed to do.
It’s also a less complex approach to flight than electric vertical takeoff and landing (eVTOL), potentially reducing cost along with engineering. Lower power requirements and less complexity generally add up to less takeoff weight, leaving capacity for more passengers or cargo.
Metro Hop’s goal is to offer electric airplanes for either role. The airplanes would weigh approximately 5,000 pounds and have a 45-foot wingspan. Mombrinie says his engineers are shooting for a 1,000 pound payload and cruise at speeds up to 2oo mph. Rather than re-charging its aircraft, Metro Hop imagines swapping batteries for fast turn-around.
“The infrastructure requirement to carry a lot of [electric] power becomes a huge problem,”
Mombrinie says, referring to the expensive, potentially dangerous high power charging facilities eVTOL operators are proposing.
Emphasizing the potential quietness of a Metro Hop aircraft – claimed to equate to an electric car – Mombrinie explains that the startup envisions landing at conventional airports but also atop or adjacent to existing warehouses or industrial complexes with large rooftop or open areas.
These areas would provide space for a “Metro Dock”, a two level structure with the top deck acting as a runway and the lower deck facilitating quick robotic cargo and passenger swaps.
“Our focus is on middle-mile parcel delivery, on hospital supplies,” Mombrinie says. “We’ve thought about doing this at shopping malls, many of which are dying out.”
ABOUT THE VEHICLE SYSTEMS, DYNAMICS, AND DESIGN LABORATORY AT AUBURN UNIVERSITY
The Vehicle Systems, Dynamics, and Design Laboratory (VSDDL) at Auburn University has extensive experience in modelling and simulation of aircraft dynamics and systems, flight simulation, and aircraft sizing and performance analysis. The lab is supported by funding from NASA Langley and Ames Research centers to investigate stability and control for novel aircraft concepts. It is also involved in multiple projects with SBC (small business concern) partners as part of the Agility Prime program.
ABOUT AGILITY PRIME
The United States Air Force recently launched Agility Prime, coining it “a non-traditional program seeking to accelerate the commercial market for advanced air mobility vehicles.”
Agility Prime also aims to bring together industry, investor, and government communities to establish safety and security standards while accelerating commercialization of this revolutionary technology. Agility Prime counts the Federal Aviation Administration as one of its partners, who sees tremendous value in this program for civil aviation applications.
Sources: Press Release; Forbes