, a high-tech race car and aerospace firm off Avenida La Pata in San Clemente’s commercial district, broke ground on a new 15,000-square-foot, $3-million manufacturing centre.
Armed with the latest design technology and poised to increase its manufacturing capacity by at least 600 percent, the firm plans to double its workforce by hiring and training 75 technicians.
Swift President Jan Refsdal said 75 new hires is a conservative estimate and the firm’s investment in San Clemente could increase to $10 million over the next five years. “We’ve been producing four to five vehicles per month, and [Northrop Grumman] is telling us to produce 30 per month,” he said.
The vehicle in question is the Bat 12 unmanned aircraft, which Swift began developing in 2009. Northrop bought the patents, then hired Swift to begin producing the craft for the US military. The Bat 12 can be launched in the field, without a runway, and is used for reconnaissance to help ground troops detect improvised explosive devices.
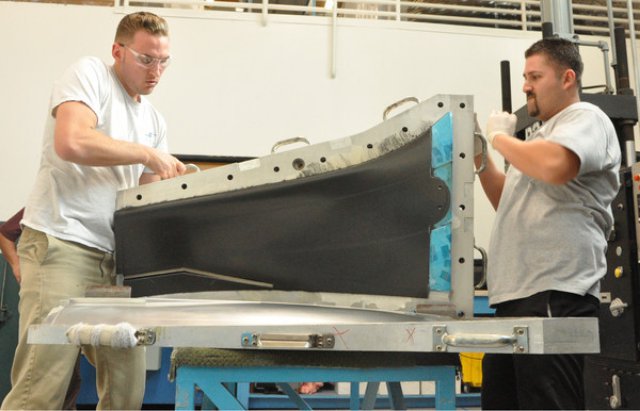
Technicians Joe Smetona, left, and Francisco Gonzales pull a composite aircraft wing out of its mold - Photo: Adam Townsend
Swift’s subcontract is part of a $26.2-million deal Northrop Grumman and the feds signed in August, according to Defense Industry Daily. Contractors in many parts of the U.S. have a piece of the pie, manufacturing different parts of the drone and launch equipment, but the Bat 12 isn’t ready to fly until it leaves the factory floor in San Clemente.
Part of what makes all of Swift’s aerospace and racing development possible is the company’s virtual wind tunnel. Swift and its bevy of technical partner companies are on the cutting edge of virtual testing technologies, doing work that used to take up an entire building in a space the size of a restaurant freezer.
In the 1990s, when Swift’s primary business was designing race cars, the company plant on the hill overlooking Avenida Pico housed a 15,000-square-foot wind tunnel with a 500-watt motor. Designed to test parts and vehicles at speeds up to 140 mph, the machine was massively expensive to run and maintain, said Swift’s chief scientist Mark Page.
Now, with a new award-winning computer system, Swift can eliminate the expense of fabricating every test part. Engineers instead load the hypothetical part’s dimensions into their virtual wind tunnel. Luo said the computer equipment designed by Cray and Netlist has the computing processor power of about 18 to 36 MacBook Pros and the RAM memory of about 107 to 215 personal computers.
The computers do about five equations per cube of air, sometimes taking all night to crunch the numbers and give operators a visual representation of how any design would work in the real world.
But Refsdal said real wind tunnels are still useful. When Swift hits on a design it thinks is workable, it hires a subcontractor to run tests in a real-life wind tunnel. Now that CFD programmes are so widely available, there is an overcapacity of wind tunnel space in the industry, making it easier and cheaper for Swift to contract out testing, he said.
Source: San Clemente Patch